Estimated Reading Time: 4 minutes
Airplane engines are marvels of modern engineering, designed to endure extreme conditions and deliver consistent performance over thousands of flight hours. For many passengers, the fear of an engine failure may linger in the back of their minds, but the truth is that modern jet engines are among the most reliable machines ever built. With advanced technology, rigorous testing, and a focus on redundancy, engine failure has become exceedingly rare.
The Engineering Behind Reliability
- Built for Redundancy
Modern jet engines are designed with multiple layers of backup systems to ensure they can continue operating even in the face of unexpected issues. For example, a typical jet engine has:
Dual or Triple Systems: Key components, such as fuel pumps, ignition systems, and sensors, are duplicated or triplicated. If one system fails, another seamlessly takes over.
Fail-Safe Design: Even in cases of partial damage, engines are built to keep functioning long enough to ensure a safe landing.
This redundancy extends beyond the engines themselves. Commercial aircraft are almost always equipped with at least two engines, and many long-haul jets have four. In the unlikely event of a single engine failure, the remaining engines are more than capable of maintaining safe flight and landing.
- Stringent Testing and Certification
Before an engine is approved for use in commercial aviation, it undergoes years of rigorous testing. Manufacturers push engines to their limits to simulate extreme conditions, such as bird strikes, severe weather, and rapid altitude changes.
One key test is the ETOPS (Extended-range Twin-engine Operational Performance Standards) certification. This ensures that twin-engine aircraft can safely operate on long overwater or remote routes, even if one engine fails. To achieve ETOPS certification, engines must demonstrate an exceptionally low failure rate and the ability to function reliably under duress.
- Advanced Materials and Design
Jet engines are constructed using cutting-edge materials that can withstand the intense heat and pressure of operation. The turbine blades, for instance, are made from nickel-based superalloys and often feature intricate cooling channels to maintain structural integrity at temperatures exceeding 1,600°F (870°C).
Additionally, modern engines incorporate:
Bladed Disk (Blisk) Technology: A combination of blades and disks into a single component, reducing the number of moving parts and increasing durability.
Digital Engine Control: Computers monitor every aspect of engine performance in real time, automatically adjusting fuel flow, airflow, and other parameters to optimize reliability.
Why Engine Failures Are So Rare
Statistically, jet engine failures are extraordinarily uncommon. On average, modern jet engines experience one failure for every one million flight hours. This is due to a combination of factors, including:
Predictive Maintenance: Airlines use advanced sensors and data analytics to monitor engine health continuously. Potential issues can be identified and addressed long before they become critical.
Quality Manufacturing: Engines are built to exacting standards, with each component undergoing meticulous inspection and testing.
Regular Inspections: Engines are inspected and maintained at precise intervals, ensuring that wear and tear never reach dangerous levels.
Real-Life Example: The “Gimli Glider”
In 1983, Air Canada Flight 143 famously ran out of fuel mid-flight due to a miscalculation, causing both engines to shut down. The pilots successfully glided the aircraft to a safe landing at a former airfield in Gimli, Manitoba. While the incident highlighted human error, it also demonstrated the aircraft’s ability to remain controllable even without engine power, thanks to aerodynamic design and redundancy in other systems.
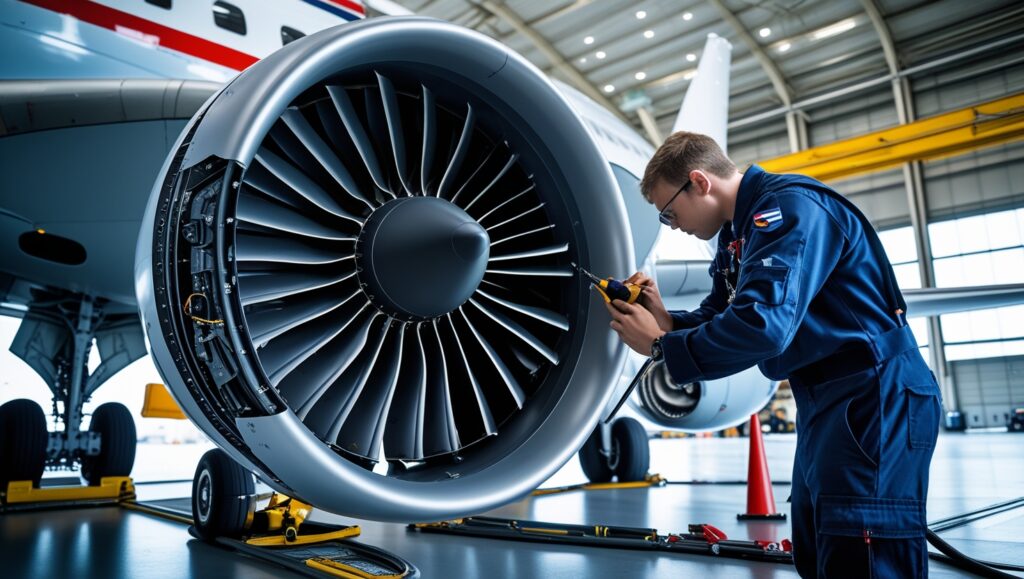
Reassuring Passengers: The Safety Net of Redundancy
Beyond the engines themselves, the safety of flying is enhanced by multiple backup systems throughout the aircraft:
Auxiliary Power Unit (APU): A small engine that provides electrical power and pressurization if the main engines fail.
Ram Air Turbine (RAT): In the event of a total power loss, the RAT deploys to generate emergency power using airflow.
Pilot Training: Pilots are extensively trained to handle engine failures and other emergencies, with regular simulator sessions to practice these scenarios.
The Future of Jet Engine Reliability
As technology continues to advance, jet engines are becoming even more reliable. Innovations such as additive manufacturing (3D printing) allow for more precise and robust components, while hybrid-electric propulsion systems promise to reduce mechanical complexity and further enhance reliability.
Moreover, sustainable aviation fuels (SAFs) are being integrated into modern engines, ensuring that reliability is paired with environmental responsibility. These fuels are tested to meet the same stringent standards as conventional jet fuel, ensuring no compromise in safety or performance.
Conclusion
The reliability of airplane engines is no accident—it’s the result of decades of innovation, rigorous testing, and a commitment to safety at every level of aviation. From their redundant designs to advanced materials and real-time monitoring, modern jet engines are engineered to keep passengers safe in even the most challenging conditions.
So, the next time you board a flight, rest assured: the engines powering your journey are among the most dependable machines in existence.